New Interceptor Makes Waves In Wet Food Inspection
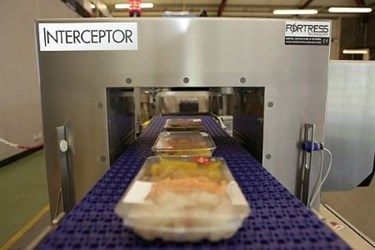
Fortress Technology has revealed an international breakthrough in food safety inspection. Increasing stainless steel detection by 100% compared to the most recent generations of metal detectors, the Interceptor accurately inspects wet and conductive products and helps to eliminate false rejects, making it one of the biggest game-changers to hit the food processing sector in recent years.
Specifically designed to tackle the longstanding challenge of high product rejects when using metal detectors to inspect meat, dairy, ready meals, bakery and fortified cereals applications, Fortress’s latest technology splits the frequency signals. This means that the machine can clearly differentiate between the signal generated by the product as a result of moisture or mineral content and any metal contaminant, putting a stop to a potential stainless steel signal being ‘swamped’ by product effect.
Although stainless steel contamination in products is a rare occurrence, the metal is prevalent in industrial food preparation equipment. “Whether you are mixing batches of bread or snack ingredients or slicing and dicing wet meat, bakery and cheese products into smaller portions using wires and knives, there’s a risk of tiny fragments entering the production chain,” comments Fortress’s Sales Director Phil Brown.
In contrast to recent metal detectors, the sensitivity of the Interceptor means it can pick up metal contaminants half the dimensional size previously identifiable. “Detection depends on the size, shape and orientation of metal particles. Although a test sample sphere isn’t a real world contaminant, a 0.5mm change in sphere size can equate to 25mm difference in wire length,” stresses Phil.
Cutting out background interference
The Interceptor builds upon the cutting-edge Simultaneous Multi-Frequency Technology introduced by Fortress some six years ago. The new technology works by carrying out a real-time analysis of a low-frequency and a high-frequency signal in parallel.
Phil explains: “Using an advanced algorithm the Interceptor is able to split the product and metal detection signals and then link the readings back together. Compared to the traditional approach where we would tune into specific frequencies, this new method means we can identify the product effect (most noticeable at lower frequencies) and eliminate it from the higher-frequency signal, where the potential effect of the metal is more prominent.”
In some cases, alternative approaches may work on up to 10 different frequencies, where the system homes in on the most relevant range. However, metal detectors that select individual frequency ranges are not able to eliminate the product effect as readily and reliably as Interceptor, claims the Fortress team.
Single pass learning is another valuable feature. Already available on the Phantom and Stealth models, the detector range instantly teaches itself and can recall the signature of a given product with a single pass, making the manufacturing process much simpler for production staff and reducing the time spent introducing and checking operational protocols.
“The combination of 100% increased metal detection sensitivity, reduced false product rejects, single pass product learning, and straightforward upgrades go a long way to boosting overall equipment effectiveness and quality assurance for food processors and manufacturers, as well as safeguarding consumers,” highlights Phil.
Mobilising smartphone technology
Sticking to the Fortress watchwords of simplicity and reliability, the Interceptor mobilises well-tried technologies in new and efficient ways. By adopting the type of microprocessing power present in today’s smartphones, the company can continue to offer customers its unique ‘Never Obsolete’ guarantee ensuring future equipment compatibility and giving more expansion options. “A few years ago this type of technology would have been far more difficult and costly to integrate into metal detectors,” adds Phil.
For additional accuracy, Fortress’s FM Software is built into the Interceptor. This brings a predictive element to the analysis of signals. In its own right, FM Software increases detection sensitivity by up to 40%.<
In true Fortress style there are no hidden extra options, meaning no financial surprises for customers. Wi-Fi and Ethernet connections are available, as is Halo automatic testing.
From a machine sustainability perspective, customers with a perfectly functional Fortress metal detector can easily upgrade to the very latest processing unit and software and integrate the new coil structure which the Interceptor’s accuracy is dependent upon.
Being IP69K rated, the new range is resistant to water ingress and dust, ensuring long-term reliability and performance in dusty and heavy washdown environments. Made to order in the UK, Interceptor units can be deployed in different locations on the production and packing line, including apertures customised to a given conveyor, pipeline configurations for pumped product and gravity systems for powders.
Like other metal detectors, the Interceptor also reliably detects the range of ferrous and non-ferrous metals, including aluminium, which continues to pose the highest metal contaminant risks in the food industry. “With the Interceptor, we can challenge traditional expectations when it comes to detection inside metallised film,” claims Phil. “This new Fortress Interceptor range comes close to the performance of x-ray, at a much lower capital investment. What’s more the Interceptor can accurately inspect products with variations in density, from bulk cuts to minced meat, or grated, sliced and block cheeses.”
For more information, visit www.fortresstechnology.co.uk.
Source: Fortress Technology